Critical Factors: Understanding and Navigating Today’s Truck Driver Shortage (Part 2 of 5)
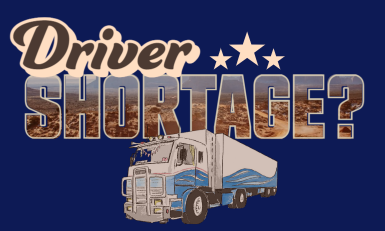
The term “supply chain” has become a part of our everyday vernacular as consumers experience empty shelves and increased prices. A lack of truck drivers is an important component of the supply chain disruptions impacting each of us.
In our first article of this series, we considered differing perspectives about the number of drivers. In this installment, we look at other critical factors contributing to this shortage.
Truck driver demographics is a contributing factor that can’t be ignored. Nearly a quarter of the current trucking workforce will hit retirement age in the next 10 years and 8 percent of drivers are already beyond retirement age, according to Emsi, an economic data and analytics firm.
“The average age of drivers is in the 50s and they’re looking at retirement—and many signed off during Covid,” explains Gail Rutkowski, executive director for the National Shippers Strategic Transportation Council. “The driver shortage is not an issue that’s going away anytime soon, especially if the current volatility in freight volume continues.”
The longstanding rule regarding driver minimum age is also an impediment to attracting a new generation of drivers.
“Truck driving is one of the few jobs that pays a decent wage for high school graduates, but they have had to wait until turning 21 to get a commercial driver’s license,” Rutkowski notes. “We’re losing the opportunity to hire 18- to 21-year-olds as truck drivers.”
Fortunately, government agencies sometimes recognize that this type of trucking regulation negatively impacts capacity and make necessary adjustments.
Rutkowski shares that the recent Infrastructure Investment and Jobs Act includes the establishment of a driver apprenticeship program for 18- to 21-year-old truck drivers.
While driver issues are the tip of the capacity shortage iceberg, there are several other contributors lurking below the waterline. It is imperative to navigate around them as well.
These challenges include well-intentioned state and federal regulations, which have had a negative impact on service availability.
Examples include California’s independent contractor legislation, which will make it very difficult for motor carriers to use owner-operators to handle fluctuations in supply and demand, and changes in safety-related hours of service rules, which lead to fleet productivity losses.
The trucking industry is not immune to the supply chain disruptions harming other economic sectors.
Much like the automotive industry, the semiconductor shortage is delaying production and delivery of new tractor trailers. Critical service parts are scarce and forcing drivers off the road while they wait for repairs.
Trailer manufacturers can’t fulfill orders fast enough to satisfy industry needs, so the net result is limited growth of capacity at a time when it is sorely needed.
“There’s been a very high number of Class 8 trucks produced and record-breaking prices on used trucks, although there is a slowdown because of the chip shortage and a lack of parts,” explains Kenny Lund, executive vice president at Allen Lund Company, LLC, headquartered in La Canada, CA.
Ryan Carter, president of Scotlynn USA Division Inc. and Scotlynn Transport LLC., has firsthand experience with these equipment issues. “We have an order for 100 new trucks that won’t be delivered until Q1 of 2023. We can’t get any in 2022 simply because the manufacturers don’t have chips or various components.”
“As far as the current fleets out there,” Carter notes, “there are availability issues with depth sensors and fuel sensors. When they fail, the truck goes down for six to eight weeks while we wait for replacement sensors. It’s a real tragedy.”
The pandemic-driven shift in demand from services to tangible goods adds to trucking capacity issues.
After a brief and tumultuous decline in spending in 2020, spending resumed at a strong pace and the economy began a rapid recovery.
There is now more freight to move than prior to the pandemic but little additional capacity available due to delays in new equipment deployment. Until this equipment is put on the road to ensure that companies get inventory levels back to normal, demand-driven capacity challenges will continue.
Source: Blue Book Services, Inc.